A multi- year maintenance plan offers you insight into the lifespan and costs of your assets. This plan is essential for the continuity of your business processes.
The effectiveness of the maintenance work carried out is greatly increased if that work is carried out punctually and systematically. A condition assessment in accordance with NEN 2767 forms the basis of this.
For buildings with numerous electrical and mechanical installations as well as structural elements, an effective multi-year maintenance plan is essential for the continuity of the business processes and thus controlling the costs. So an objective condition assessment that is registered and reported on is extremely important.
This also offers quality control and, last but not least, inspects the maintenance work carried out.
That inspection of the maintenance, repair or replacement work is very important. It makes it possible to assess whether the policy conducted has effectively led to the desired condition. This inspection may coincide with updating the inventory of the components of the buildings and installations or the next condition assessment.
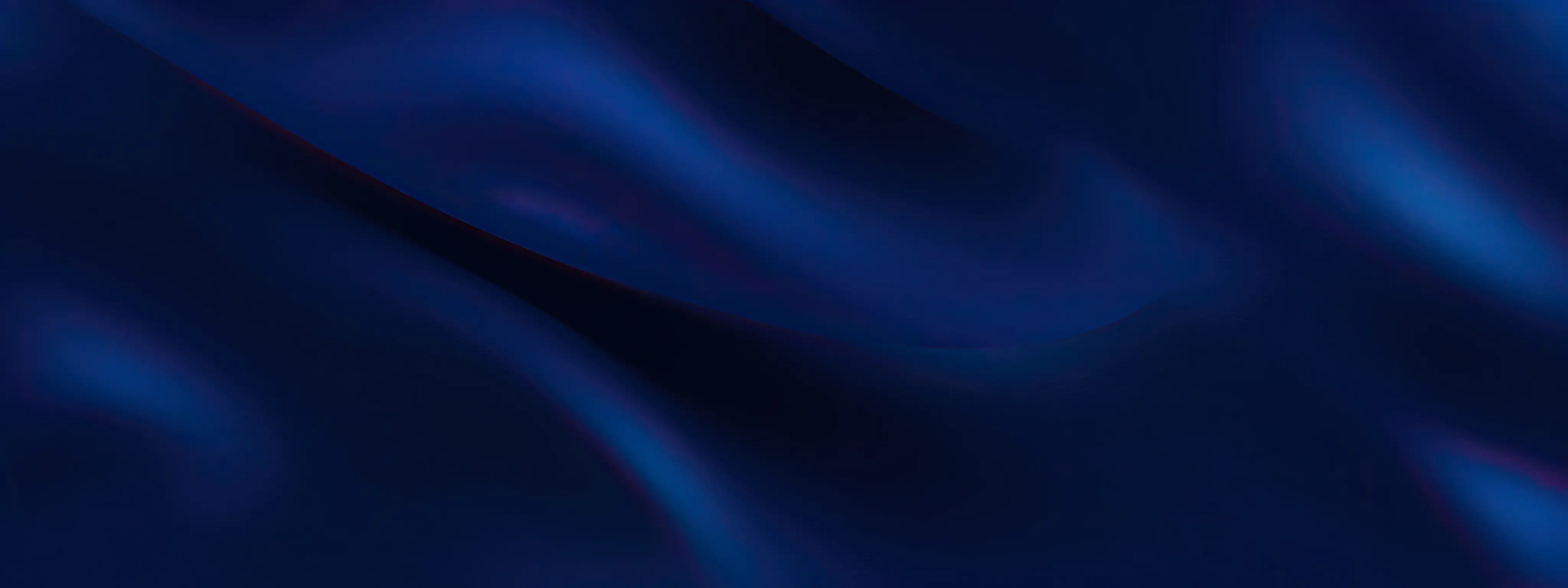
Talk to our experts
How and how often should a multi-year maintenance plan be updated?
A multi-year maintenance plan starts with an inventory of the elements that should be included, elaborated to the level of detail you wish within your maintenance policy.
Activities are then included on the basis of the condition ascertained (condition assessment) in relation to the desired condition. Not based on gut feelings, but clearly substantiated. And when finally it is determined which activities should be carried out in which year, the costs involved can also be calculated.
This is all done with software in which a multi-year plan with supporting report can be generated.
The frequency with which a multi-year maintenance plan should be updated has not been determined in the standard. Since a multi-year maintenance plan is a dynamic process, we recommend that it be updated at least every three to four years.
Want more information about our multi-year maintenance plan?
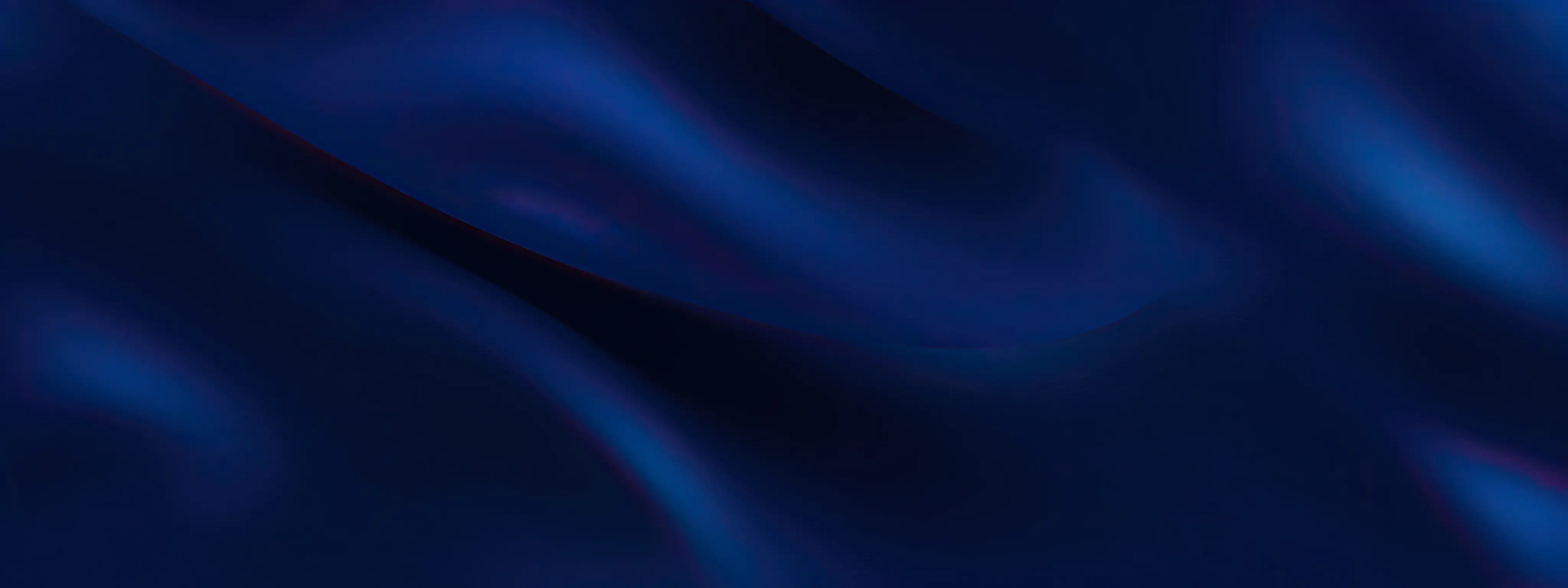